Collaborators: P. J. Ponce de Leon, F. A. Hill
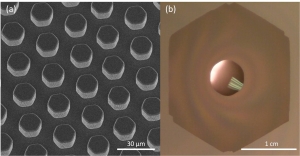
Electrospun nanofibers’ unique properties promise to make them a key engineering material across many disciplines. Due to their high specific surface area and porous aggregation, they are highly desirable as scaffolds for tissue engineering, layers in multi-functional protective clothing, catalyst dispersers in hydrogen fuel cells [1], and more. Electrospinning is the technique of generating nanofibers using strong electric fields applied to polar, high-molecular-weight polymeric liquids. It is the only known process that can generate fibers of arbitrary length with controlled morphology down to the 10-500 nm diameter range and has tremendous versatility as it can create non-woven or aligned mats of polymer, ceramic, semiconductor, and/or metallic fibers.
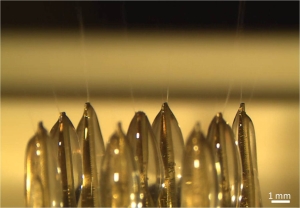
This work addresses the most pressing problem in manufacturing nanofiber-based technologies, namely, the low throughput of traditional single-needle electrospinning. We implement multiplexed, externally-fed fiber emitters to increase throughput while circumventing pressure losses and complexity associated with internally-fed systems [2][3]. We fabricate linear emitter arrays that consist of pointed structures etched out of silicon by DRIE and assemble these into a slotted base to form a planar array. By altering the surface chemistry and roughness of the emitters, we can modify their wetting properties to enable “hemi-wicking” [4] of fluid through the micro-texture (Figure 1). The emitter geometry determines local electric field enhancement. The interplay between electric and surface tension forces governs the fluid transport and fiber formation.
We have performed characterization of nanofiber production from polyethylene oxide (PEO) in ethanol/water mixtures at voltages ranging from 5-30 kV and electrode distances ranging from 1-10 cm. Video footage reveals fiber production from multiple emitters (Figure 2) and SEMs confirm PEO fibers with average diameters as low as 100 nm. Future work includes electrospinning from higher density emitter arrays and incorporation of a proximal extractor electrode to improve emission uniformity.
References
[1] V. Thavasi, G. Singh and S. Ramakrishna, “Electrospun nanofibers in energy and environmental applications,” Energy Environ. Sci., vol. 1, pp. 205-221, 2008.
[2] S. A. Theron, A. L. Yarin, E. Zussman and E. Kroll, “Multiple jets in electrospinning: Experiment and modeling,” Polymer, vol. 46, no. 9, pp. 2889-2899, 2005.
[3] Y. Srivastava, M. Marquez and T. Thorsen, “Multi-jet electrospinning of conducting nanofibers from microfluidic manifolds,” J. Appl. Polym. Sci., vol. 106, pp. 3171-3178, 2007.
[4] D. Quéré, “Wetting and Roughness,” Annu. Rev. Mater. Res., vol. 38, pp. 71-99, 2008.