Current Collaborators: C. Livermore (MechE), L. Gu (MechE), S. Davis (PSI), S. Lee (PSI), W. T. Rawlins (PSI)
Former Collaborators: T. Hill (Ph.D. EECS’08), B. Wilhite (UCONN), A. Epstein (Aero/Astro), Klavs Jensen (ChemE/DMSE)
Funding: DARPA, MDA
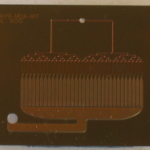
We are interested in efficient ways to produce singlet delta oxygen because it is a valuable reactant for organic synthesis and as an energy carrier for the chemical oxygen–iodine laser (COIL). COIL is attractive for applications that require very high average power, light weight, and overall system compactness. COILs are a promising alternative to CO2 lasers for industrial processing because COL lasers emit a smaller wavelength than CO2 lasers, resulting in more efficient coupling to metals and smaller spot size. Also, in a flowing gas laser such as the COIL, the waste heat flows out with the exhaust gas stream. Therefore, the laser’s average power is not limited by cooling, as are most high-energy solid-state lasers.
Singlet delta oxygen can be synthesized through the highly exothermic multiphase reaction of gaseous chlorine buffered with helium with an aqueous mixture of concentrated hydrogen peroxide and potassium hydroxide. The laser application of singlet delta oxygen generation requires a high yield to sustain laser emission, where yield is defined as the fraction of product oxygen in the singlet oxygen state. Once produced, singlet
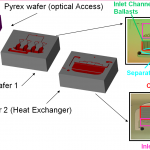
delta oxygen deactivates into ground-state oxygen by collisions with gases or solid surfaces. Thus, the reactor design must provide large surface areas for initial singlet deltas oxygen generation, followed by rapid separation of gas and liquid phases. The output gas must be maintained at low pressures to minimize homogeneous deactivation, and the reactor must be maintained at low temperatures to minimize water vaporization.
We have developed a MEMS-based singlet oxygen generator (SOG) chip (Fig. 1) that has a set of six key characteristics that enable high performance:
- The chip has a large surface-to-volume ratio that enhances reactant mixing and facilitates excess heat removal.
- The device has no moving parts for better reliability.
- The singlet delta oxygen is separated very quickly so there is a short distance from the point of formation to the point of utilization to reduce the deactivation losses.
- The chip as integrated a microfabricated heat exchanger that allows better control of the reaction.
- The device has a capillary gas–liquid separator that permits orientation-independent operation or even operation in zero gravity.
- The chip is batch-fabricated using microfabrication techniques
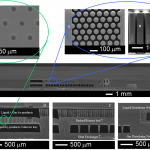
The MEMS SOG is made of a three-wafer stack (Fig. 2): a top Pyrex wafer for optical access, a middle silicon wafer that contains the ballasted chemical reactors, the distribution network for the liquid reactants, and the liquid-gas separator, and a bottom silicon wafer that contains the heat exchanger and the distribution network for the gas reactants. The chip has as liquid-gas separator a capillary array. The reactor is a backed bed of high aspect-ratio columns that enhance mixing of the liquid and gas reactants. Selected views of the different parts of the MEMS SOG are shown in Fig. 3
Fig. 2. Exploded view of the MEMS SOG.
Fig. 3 Selected views of the MEMS SOG: detail of liquid-gas separator (upper left); detail of the reaction chamber (upper center and upper right); cross section of the MEMS SOG (middle); cross-section of the liquid-gas separator (lower left); cross-section of a reactor on top of the heat exchanger (lower center); cross section of distribution network(lower right).
Figure 4 shows a packaged SOG chip producing singlet delta oxygen. The red glow in the optical cell corresponds to the formation of as the decay emission to ground state of an excited dimol formed from two singlet delta oxygen molecules. IR spectroscopy of the emission shows a peak at 1.27 mm, which is the decay to ground state of the singlet delta oxygen molecule (Fig. 5). The data also shows that the chip reaches steady state very quickly. The MEMS SOG can produce singlet delta oxygen with yield better than 80% and molar flowrates of singlet delta oxygen per unit of reactor volume exceeding 6×10-2 mol.L-1.s-1
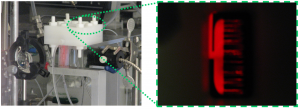
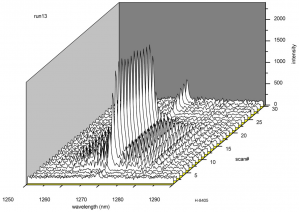