Current Collaborators: F. Eid (MechE), C. Livermore (MechE)
Funding: DARPA/MTO
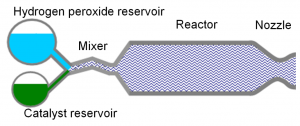
We are interested in scaled-down MEMS hydrogen peroxide steam generators because we are interested in developing high-performance portable pump systems and efficient chemical rockets for nanosatellites:
- Scaled-down hydrogen peroxide steam generators can be used as ejector pumps. Compared with existing MEMS pumps for gases, ejector pumps offer much higher flow rates for a given pressure rise, along with robust operation and no moving parts. In an ejector pump, a high-speed gas stream mixes with a low-speed stream to produce pumping of the low-speed stream by transformation of part of the mixed flow’s kinetic energy into pressure rise.
- In addition, the hydrogen peroxide steam generator can be connected to a converging-diverging nozzle and thus implement a green monopropellant rocket to produce impulsive thrust for nanosatellites. Hydrogen peroxide is a green alternative to state-of-the-art hydrazine monopropellants.
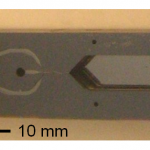
In our reactor we use aqueous high-test hydrogen peroxide for the chemical generation of steam using a catalyst. Hydrogen peroxide decomposes catalytically to produce oxygen gas, water, and heat that subsequently vaporizes the water. Unlike most microfabricated hydrogen peroxide reactors reported, we use a liquid (homogeneous) catalyst instead of a solid (heterogeneous) catalyst. Heterogeneous catalysts need very narrow flow channels to maximize the reaction surface area, which can make the chip prone to clogging. Also, a heterogeneous catalyst is susceptible to poisoning by stabilized peroxide and eventually becoming ineffective. In a portable pump application, these handicaps could strongly affect the lifespan and reliability of the system. As a trade-off, chemical reactors that use homogenous catalysts require a mixer. The system is completed by a converging-diverging nozzle that accelerates the steam to a desired speed (Fig. 1).
One of the challenges with microscale chemical reactors is that, as the size is reduced, the increase in the surface area-to-volume ratio could make the heat losses comparable to the heat generated by the exothermic reaction inside the device. Therefore, the energy remaining inside a scaled-down hydrogen peroxide reactor may not be sufficient for sustaining the reaction and achieving full
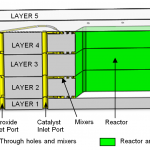
vaporization of the water produced. We addressed this challenge by using multi-domain physical modeling to simulate the reacting flow and evaluate the heat losses from the device. We used the simulation results to guide the design of both a MEMS device that decomposes hydrogen peroxide using a homogeneous catalyst and a package with sufficiently high thermal resistance to enable full peroxide decomposition and complete water vaporization.
We developed a scaled-down MEMS hydrogen peroxide steam generator that is suitable for batch fabrication (Fig. 2). The chip is fabricated using a five-wafer stack (Fig. 3). Layers 1 through 4 are silicon wafers; layer 5 is a Pyrex wafer that caps the device and provides optical access. Layer 1 contains the inlet holes for the peroxide and catalyst streams along with thermocouple insertion holes to measure the silicon wall temperature. Layer 3 contains through holes and some of the reactor and nozzle depths. Layers 2 and 4 are identical, and they contain the relatively shallow mixers on both sides of each layer in addition to the remaining deep-etched features. The chip is made using contact photolithography, DRIE, fusion bonding, and anodic bonding. As shown in Fig. 3, the mixers are multiplexed to achieve both high mixing performance and high flowrate throughput for a given pressure loss across the mixer. Our device is the first reported scaled-down hydrogen peroxide steam generator that is able to fully decompose hydrogen peroxide. We used refractive index analysis to confirm full peroxide decomposition, and we used visual inspection and temperature measurements to confirm full water vaporization. Based on modeling and experimentation, wall temperatures as high as 650 K are achieved for 84% hydrogen peroxide concentration (Fig. 4), and initial hydrogen peroxide concentrations of 74% or higher are needed to achieve full peroxide decomposition.
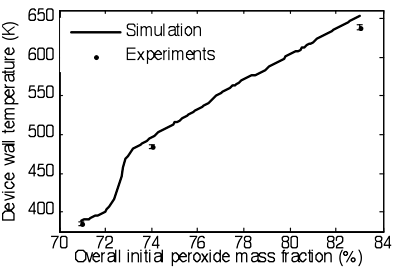